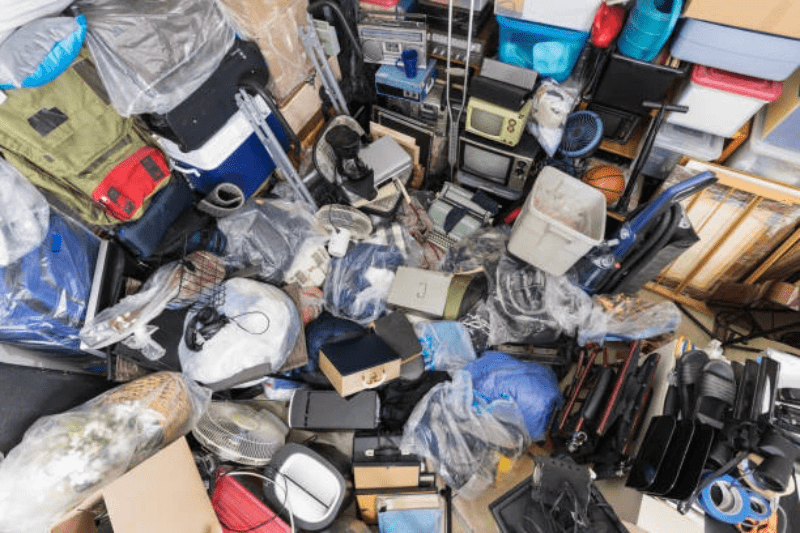
When it comes to managing logistics, unloading and stockpiling play a crucial role in minimizing delays and maximizing operational efficiency. Whether you are handling goods for a warehouse or working in distribution, streamlining these processes can have a significant impact on your business's overall productivity. In this article, we will delve into some highly effective strategies that will help you optimize your unloading and stockpiling operations.
Planning for Success
Before diving into unloading and stockpiling, it is essential to establish a comprehensive plan. By outlining your objectives and implementing efficient strategies from the start, you can save time, reduce costs, and avoid potential bottlenecks. Here are a few key aspects to consider in your planning process:
1. Prioritize Inventory: Categorize your inventory based on urgency and demand. Prioritizing high-demand products can ensure they are readily available for immediate shipment or distribution.
2. Proper Equipment: Identify the required equipment and tools for unloading and stockpiling. By having the right equipment on hand, you can streamline the entire process and minimize potential delays.
3. Space Optimization: Analyze your available space and design a layout that maximizes efficiency. Consider factors such as aisle size, pallet stacking techniques, and flow patterns to minimize travel distances and enhance overall accessibility.
Unloading Best Practices
Efficient unloading is the first step towards seamless operations. By implementing the following best practices, you can significantly streamline the unloading process:
1. Proper Staffing: Ensure you have an adequate number of trained personnel available for unloading tasks. By having a well-organized team, you can minimize errors and avoid unnecessary delays.
2. Unloading Sequence: Establish a clear and logical sequence for unloading. For example, start with products that require immediate attention or have strict delivery deadlines. This approach ensures a smooth transition from unloading to subsequent processes, such as quality control or stockpiling.
3. Advanced Technology: Implement technology solutions such as barcode scanning or Radio-Frequency Identification (RFID) to facilitate the process of recording and tracking unloaded products. Utilizing modern technology can significantly reduce errors and enhance overall efficiency.
Stockpiling Techniques
Efficient stockpiling not only ensures optimal use of available space but also facilitates easy retrieval and loading processes. Consider the following techniques to enhance your stockpiling operations:
1. First-In, First-Out (FIFO): Adhering to the FIFO principle eliminates the risk of expired or obsolete inventory. Arrange your stockpile so that the oldest products are easily accessible and will be utilized first.
2. Space Optimization: Utilize vertical space wisely by stacking goods safely and efficiently. Use sturdy pallets and consider investing in vertical storage equipment such as racks or mezzanines to maximize storage capacity.
3. Clear Labeling: Properly label each stockpile with essential information such as product name, batch number, and expiration date. Clear labeling ensures easy identification, reduces search time, and prevents mistakes during retrieval.
Continuous Improvement
To ensure a consistently efficient unloading and stockpiling process, it is crucial to embrace a mindset of continuous improvement. Regularly assess your operations, identify areas for enhancement, and implement changes accordingly. Here are a few strategies to foster ongoing improvement:
1. Data Analysis: Regularly analyze data related to unloading and stockpiling to identify patterns or trends. This analysis can help you refine your processes, optimize resource allocation, and eliminate any bottlenecks.
2. Employee Training: Invest in ongoing training for your staff to enhance their skills and keep them up-to-date with best practices and new technologies. Well-trained employees can adapt more effectively to changing circumstances and contribute to improved efficiency.
3. Collaborative Efforts: Engage with your suppliers, customers, or logistics partners to identify potential areas for collaboration and improvement. By fostering open communication and sharing insights, you can optimize the entire supply chain process.
In conclusion, successful unloading and stockpiling go hand in hand with efficient logistics management. By implementing effective planning strategies, following best practices for unloading and stockpiling, and embracing continuous improvement, you can optimize your operations, reduce costs, and enhance overall productivity. Remember